Objectives:
- Design of a Francis Turbine runner for a hydropower plant.
project Team:
Principal Investigator | Dr. Manish Pokharel | KU |
Project Leader | Dr. Sailesh Chitrakar | KU |
Researcher | Mr. Amul Ghimire | KU |
Project Date | December, 2021 – March, 2022 |
|
Funding Agency | Undisclosed Hydropower Project |
|
Summary
Sediment erosion is one of the major problems faced by hydropower projects in Nepal. A newly commenced hydropower project from Eastern Nepal faced such problems and contacted the lab to conduct a study and produce a Francis turbine runner for the turbine which is less susceptible to sediment erosion. The project was initiated to design a Francis turbine runner for an existing Francis turbine. Thus the very first challenge was to design the runner that fits exactly into the previous runner’s space. Operational drawings available at the power plant were referenced to make sure that the dimensions of the turbine was good enough to fit the turbine space.
Upon studying the images received from the site, it was evident that the sediment erosion was se-vere both on turbine as well as the guide vanes. Moreover, the peculiar erosion pattern on the guide vane facing ends suggested that erosion could have been caused due to the leakage flow through clearance gap. However, the client’s major requirement was to have a spare runner that is more resistant to sediment erosion. Thus, optimization was performed on the runner only.
In order to start the optimization, the meridional passage was first developed based on design data and drawings available. Main Dimensions like: inlet diameter, outlet diameter, inlet height and overall height of the runner were kept constant, whereas, the blade angle distribution and the out-let blade angle were used as the design parameters. While the design samples were generated using the Latin Hypercube sampling technique, a Response Surface Model was pre-pared based on the results obtained from the Numerical simulations of those design samples. Fi-nally the design parameters were optimized for minimum sediment erosion and maximum effi-ciency using modified Non-dominated Sorting Genetic Algorithm. Manufacturing drawings were later produced for the optimized design and were delivered to the clients. In addition to that it has also been recommended that much better results can be obtained by changing the guide vane design.
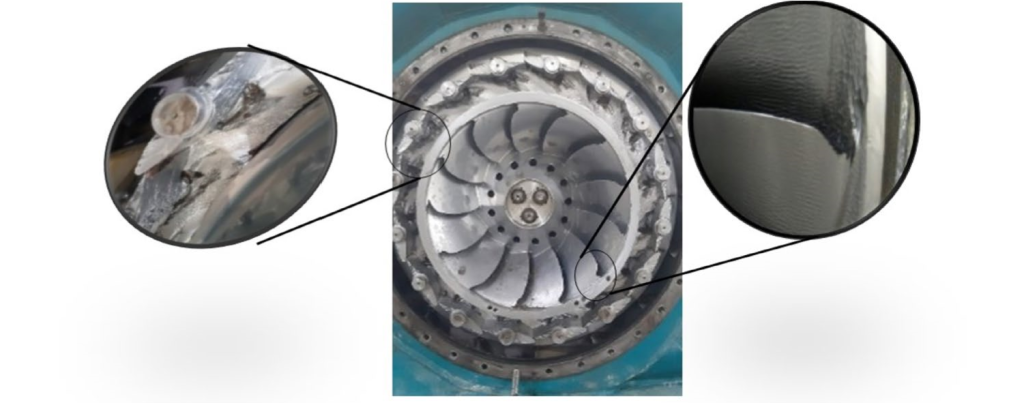
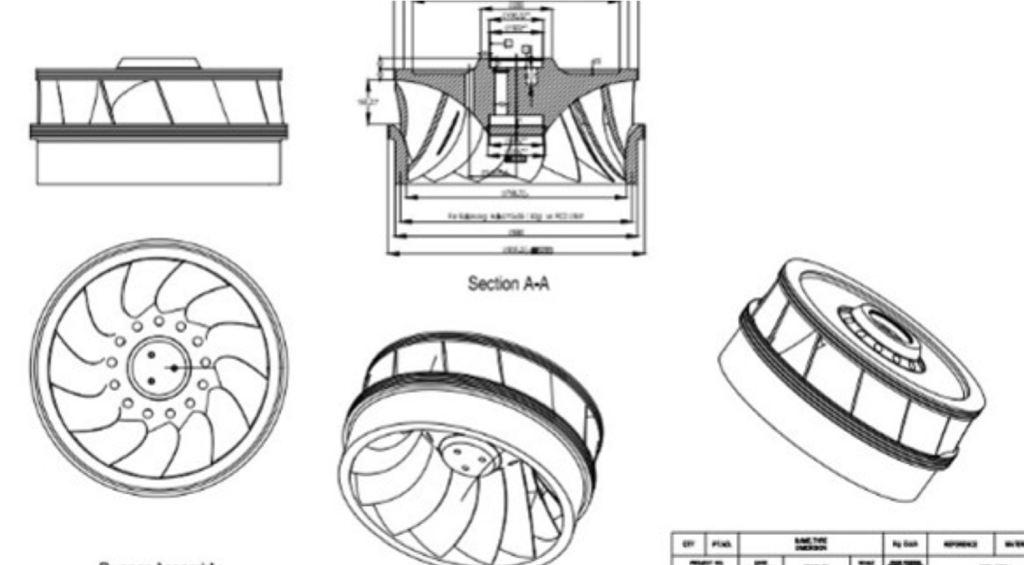